FIBRA CATIONICA

HISTORIA
VAN BRUSSEL-VERRAEST,
Dorine, Lisa; (NL). BESEMER, Arie, Cornelis; (NL).
Es un fibra de celulosa catiónica que contiene entre 1 y 30 grupos catiónicos y entre 0,1 y 20grupos aldehído por 100 unidades de anhidroglucosa, lo que constituye una base apropiadapara la fabricación de productos de papel y tejidos sin el uso de polímeros no biodegradablestales como aditivos de resistencia catiónicos. Esta fibra de celulosa catiónico se puede obtenerpor oxidación de la fibra con el fin de introducir grupos aldehído, seguido de la reacción de una parte de los grupos aldehído con un reactivo que contiene nitrógeno tal como hidrocloruro dehidrazida de betaína. Esta fibra se combina preferentemente con un polímero aniónico, talcomo almidón de monoaldehıdo carboxilo, o ciclodextrina aniónica.
Es un fibra de celulosa catiónica que contiene entre 1 y 30 grupos catiónicos y entre 0,1 y 20grupos aldehído por 100 unidades de anhidroglucosa, lo que constituye una base apropiadapara la fabricación de productos de papel y tejidos sin el uso de polímeros no biodegradablestales como aditivos de resistencia catiónicos. Esta fibra de celulosa catiónico se puede obtenerpor oxidación de la fibra con el fin de introducir grupos aldehído, seguido de la reacción de una parte de los grupos aldehído con un reactivo que contiene nitrógeno tal como hidrocloruro dehidrazida de betaína. Esta fibra se combina preferentemente con un polímero aniónico, talcomo almidón de monoaldehıdo carboxilo, o ciclodextrina aniónica.
OBTENCIÓN
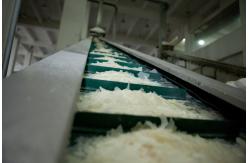
La fibra celulósico
catiónico se puede obtener por oxidación de la fibra para introducir grupos
aldehído, seguido de la reacción de una parte de los grupos aldehído con un
reactivo que contiene nitrógeno tal como hidrocloruro de hidrazida de betaína.
La fibra se combina ventajosamente con un polímero aniónico tal como carboxilo
monoaldehıdo-almidón o con ciclodextrina aniónica.
PROPIEDADES
- Tensión de fluencia, DS =0,45.
- Módulo elástico de suspensión determinados como una función de la concentración de polímero para diferentes condiciones.
- Alta transparencia, aunque admite cargas de colorantes.
- Alta resistencia al desgaste y corrosión.
- Muy buen coeficiente de deslizamiento.
- Buena resistencia química y térmica.
- Muy buena barrera a CO2, aceptable barrera a O2 y humedad.
- Compatible con otros materiales barrera que mejoran en su conjunto la calidad barrera de los envases y por lo tanto permiten su uso en mercados específicos.
- Reciclable, aunque tiende a disminuir su viscosidad con la historia térmica.
- Aprobado para su uso en productos que deban estar en contacto con productos alimentarios.
USOS
*Las fibras catiónicas se
pueden mezclar con fibras celulósicas regulares o material polimérico
hidrocoloidal para darles mejores características.
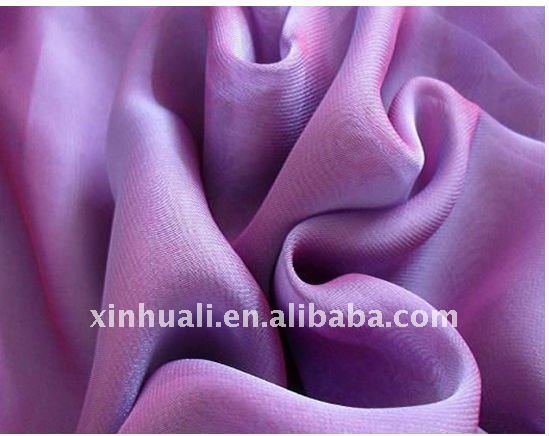
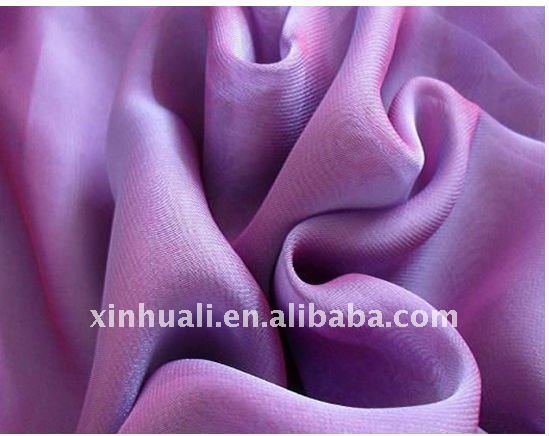